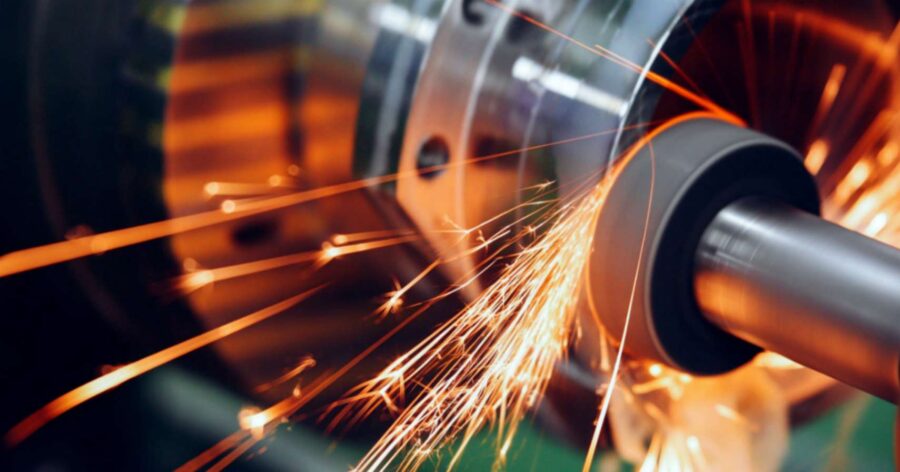
Advantages of CNC Machining Connections for Forged Pressure Vessels
CNC (Computer Numerical Control) machining connections for forged pressure vessels offer several advantages, making them a preferred choice in industries where pressure vessels are essential, such as in the petrochemical, chemical, pharmaceutical, and food processing sectors. Here are some of the key advantages:
Precision and Accuracy: CNC machining allows for the production of extremely precise and accurate connections. This is critical for ensuring that all parts fit perfectly, which is essential for the integrity and safety of pressure vessels.
Consistency: Unlike manual machining, CNC machining can reproduce the same connection over and over with minimal deviation. This consistency is crucial for large-scale production where every component needs to match perfectly with others.
Efficiency: CNC machines can operate continuously over long periods without the need for breaks or shifts changes, significantly increasing production speed. Additionally, CNC machining can reduce the time needed for setup and transition between different tasks.
Versatility: CNC machines can produce connections of almost any shape and size, making them suitable for a wide range of pressure vessel designs. This flexibility allows manufacturers to meet specific customer requirements more easily.
Material Savings: The precision of CNC machining reduces material waste, as components are made exactly to specifications. This not only saves on material costs but also supports sustainability efforts by minimizing waste.
Improved Safety: The accuracy and reliability of CNC-machined connections contribute to the overall safety of pressure vessels. Properly fitting components reduce the risk of leaks or failures under pressure, which is critical in applications involving hazardous materials.
Reduced Labor Costs: Although CNC machines represent a significant initial investment, they can reduce the need for skilled labor since the machines do the majority of the work once programmed. This can lead to long-term savings in labor costs.
Enhanced Surface Finish: CNC machining can achieve superior surface finishes on connections, which is important for sealing and longevity of pressure vessels. A better surface finish can reduce the likelihood of corrosion and improve the efficacy of seals.
Customization: With CNC machining, customizing connections for special requirements is more feasible. This allows for the design and production of unique components that fit specific applications, providing solutions that standard connections cannot.
Integration with Modern Design and Manufacturing Processes: CNC machining fits seamlessly into modern CAD (Computer-Aided Design) and CAM (Computer-Aided Manufacturing) processes. This integration facilitates the rapid transition from design to production, further speeding up the development of new products.
By leveraging the advantages of CNC machining for the connections of forged pressure vessels, manufacturers can achieve higher quality, efficiency, and safety in their products, which are essential factors in maintaining competitiveness and meeting stringent industry standards.