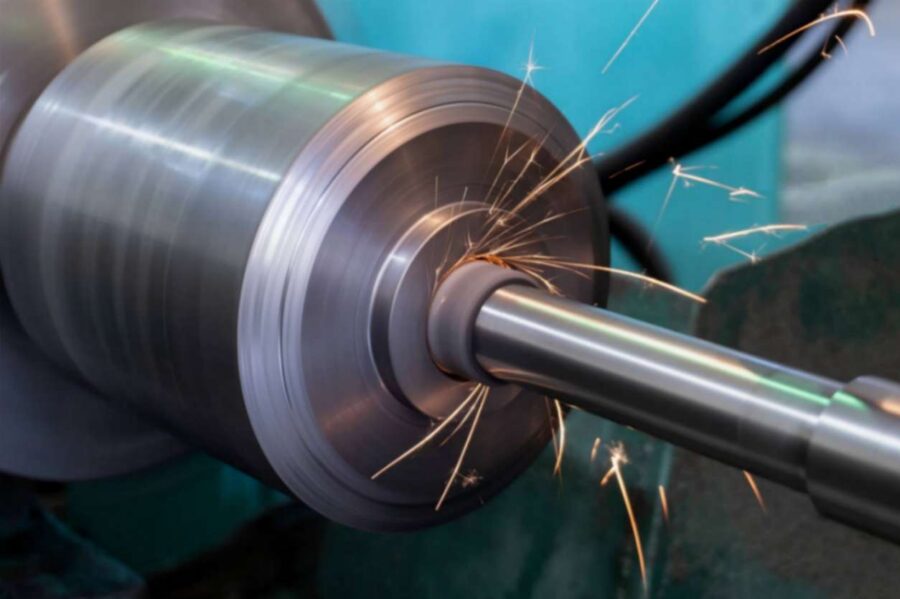
What are the Innovative Technologies Enhancing the Efficiency of Forging Pressure Vessel Components
Innovative technologies are significantly enhancing the efficiency, safety, and performance of forged pressure vessel components used in critical applications across various industries. Here are some key advancements:
Automated Forging Techniques
Automation has revolutionized the forging process with precise control over temperature, pressure, and deformation rates. Automated forging presses and handling systems minimize human intervention, reducing errors and increasing repeatability. This ensures consistent quality and structural integrity in pressure vessels, essential for their safe operation under high-pressure conditions.
Advanced Non-Destructive Testing (NDT) Methods
Recent advances in non-destructive testing, such as phased array ultrasonics and 3D radiography, allow for more detailed inspection of pressure vessels. These methods can detect flaws and inconsistencies that traditional testing might miss, ensuring that each vessel meets stringent safety standards before it is put into service.
High-Performance Materials
The development and use of high-performance materials, including advanced steel alloys and composites, are crucial. These materials can withstand extreme temperatures and pressures, resist corrosion, and have improved fatigue life. Innovations in material science often lead to lighter, more durable pressure vessels capable of handling more strenuous conditions.
Heat Treatment Innovations
Enhanced heat treatment processes like induction hardening and controlled quenching improve the mechanical properties of the forged parts of pressure vessels. These treatments ensure the metal has the necessary hardness, toughness, and strength to handle high pressures, contributing to the vessel’s overall safety and longevity.
Simulation and Modeling
Advanced simulation software enables manufacturers to model forging processes and the operational behavior of pressure vessels under various conditions. These simulations help optimize designs and forging parameters, reducing the need for physical prototypes and ensuring the vessel’s performance before manufacturing begins.
Environmental Technologies
Implementations like waste heat recovery systems in the forging process or the use of renewable energy sources help reduce the environmental impact of manufacturing pressure vessels. These technologies not only improve the efficiency of the process but also align with global sustainability goals.
These technologies collectively enhance the manufacturing and operational efficiency of forged pressure vessel components, ensuring they meet the evolving demands of industries requiring high safety and reliability standards.