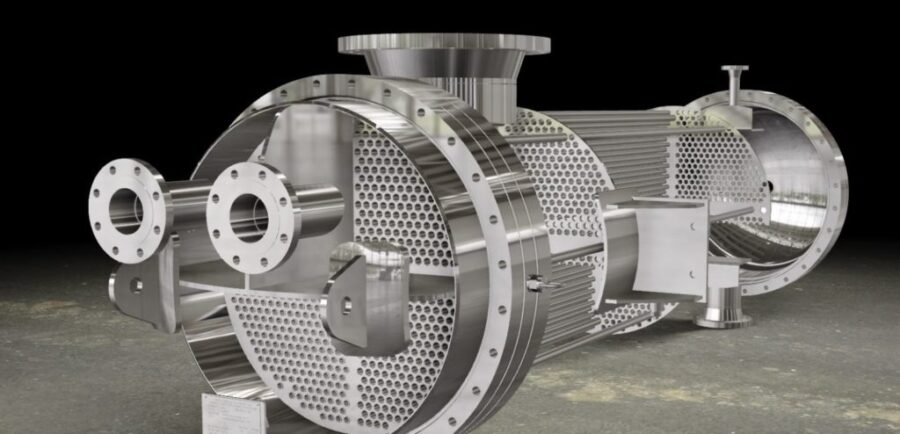
What is a Shell and Tube Heat Exchanger?
Heat exchangers are essential devices for use in the petrochemical, and power generation, among other applications. They transfer heat energy from one working fluid to another one. The fluids can be liquids, but they can also be gases and solids. One of the most popular options for this topic is shell and tube heat exchangers. As the leading forged tubesheet supplier, our team at Forged Components shares more about what you need to know about shell and tube heat exchangers.
A Look at Shell and Tube Heat Exchangers
The shell and tube heat exchangers’ design focuses on the principle of hot fluid that flows around the cooler liquid. This causes the transfer of heat that goes in the cold flow direction.
Shell and tube heat exchangers are a variety of heat exchangers that create thermal contact with a pair of working fluids through tubes. These tubes sit inside a cylindrical shell on the outside.
The popularity of shell and tube heat exchangers is related to the flexibility they offer designers when it comes to temperatures and pressures across a wide range. The two primary categories for shell and tube heat exchangers are those used in the power industry and in the petrochemical industry.
How Do These Heat Exchangers Work?
The ability to pass hot fluid through a cold fluid is the essential point of shell and tube heat exchangers. Through this design, heat exchanges without any mixing of the liquids. Each fluid starts at its own inlet and then exits at its own outlet. The flow going through the tube side goes through the tube bundle. It then exits through the tube outlet.
Each tube in a shell and tube heat exchanger has an insert called a turbulator. This turbulator causes a flow through the tubes that stops the depositing of sediment.
It is also important to note that shell and tube heat exchangers can be single or two-phase. The single-phase variety keeps a constant fluid phase during the entirety of the process. The two-phase type involves a phase change that occurs during heat transfer.
The Different Types of Shell and Tube Heat Exchangers
There are several primary types of shell and tube heat exchangers. The standard varieties are under the regulation of the Tubular Exchangers Manufacturers Association. The organization splits the designs of exchangers into three primary parts. These are the shell, the front end heater, and the rear end header. The three most popular shell and tube heat exchanger models are:
- Fixed Tube Sheet Exchangers– Fixed tube exchangers utilize a pair of stationary tube sheets. They are welded directly to the shell. These models are the most cost-effective options for shell and tube heat exchangers.
- U-Tube Heat Exchangers– U-tube heat exchangers get their name from the U shape of their tube bundle. These continuous tubes attach to the shell by using a single tube plate.
- Floating Head Exchangers– These heat exchangers combine vital aspects of the fixed tube and U-tube exchangers. While one of the tubes stays stationary to the fixed tube sheets housing, the other side uses a floating tube sheet component to expand.
The Design Behind Shell and Tube Heat Exchangers
The design of shell and tube heat exchangers involves components that include:
- Channels/Heads– The types of channels or heads used depends on the tube heat exchanger and the shell.
- Shell– These are composed of welded metal plates or pipes and can withstand extreme temperatures while corrosion resistant.
- Tubes– are either extruded or welded and composed of stainless steel, copper, carbon steel, Inconel, or titanium.
- Expansion Joint– The expansion joint is designed to effectively exchange heat from a hot substance to a cold one on the other side.
- Tube Sheet– A sheet or plate with holes that allow for the insertion of tubes or pipes.
- Tube Pitch– The distance from the middle of a tube to the center of an adjacent one.
- Baffles– Used to direct flow in the tube and shell sides to increase its velocity sufficiently.
- Tie Rods and Spacers– Structural components/supports that hold the baffles in place while maintaining space.
Shell and Tube Heat Exchanger Benefits
The benefits of shell and tube heat exchangers include:
- The ability to handle a wide range of temperatures
- Cost-effective
- They can withstand extreme variances in pressures
- They allow for thermal expansion
- They are good at preventing pressure loss
- They can be adapted/adjusted
- Anodes create a protective film
As the industry leading ASME pressure vessel connections and custom forgings manufacturer, our team at Forged Components is ready to provide you with consultation on our products and services. Please reach out to our sales team today at (281) 441-4088 or contact us online to get a quote. We look forward to providing you with the answers to any of your questions and/or inquiries.