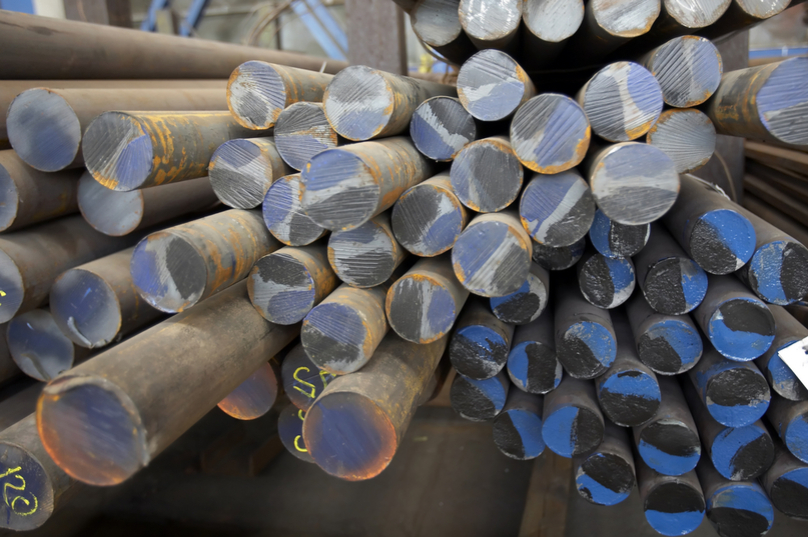
Types and Uses of Alloy Steel
API wellhead component manufacturing projects sometimes require steel with specific properties. Alloy steel combines carbon steel with other materials such as aluminum, nickel, or copper to fit the specifications of a project. Alloy steel is primarily categorized by alloy or alloy percentage.
High-Alloy Steel
High-alloy steels are defined by a high percentage of alloying elements. The most common high-alloy steel is stainless steel, which contains at least 12 percent chromium. Stainless steel is generally split into three basic types: martensitic, ferritic, and austenitic. Martensitic steels contain the least amount of chromium, have a high hardenability, and are typically used for cutlery. Ferritic steels contains 12 to 27 percent chromium and are often used in automobiles and industrial equipment. Austenitic steels contain high levels of nickel, carbon, manganese, or nitrogen and are often used to store corrosive liquids and mining, chemical, or pharmacy equipment.
Low-Alloy Steel
Low-alloy steels have a much lower percentage of alloying elements, usually 1 to 5 percent. These steels have very different strengths and uses depending on the chosen alloy. Large diameter flanges manufacturers typically choose alloys for a specific mechanical property. The variety of potential alloys makes low-alloy steel useful for a variety of projects, including seamless rolled ring forging and studding outlet manufacturing.
Type by Alloy
Alloy steel is often categorized based on the type of alloy and its concentration. These are a few of the most common additions to alloy steel:
- Aluminum removes oxygen, sulfur, and phosphorus from steel.
- Bismuth improves machinability.
- Chromium increases wear resistance, hardness, and toughness.
- Cobalt increases stability and encourages the formation of free graphite.
- Copper improves hardening and corrosion resistance.
- Manganese increases hardenability, ductility, wear resistance, and high-temperature strength.
- Molybdenum lowers carbon concentration and adds room-temperature strength.
- Nickel improves strength, corrosion resistance, and oxidation resistance.
- Silicon increases strength and magnetism.
- Titanium improves hardness and strength.
- Tungsten improves hardness and strength.
- Vanadium increases toughness, strength, corrosion resistance, and shock resistance.
Do You Need Pressure Vessel Nozzle Manufacturing?
If you need subsea connections manufacturing, long weld neck nozzle forging, or studding outlets for industrial flanges, then contact Forged Components, Inc. today. Call us at (281) 441-4088 or contact us online.