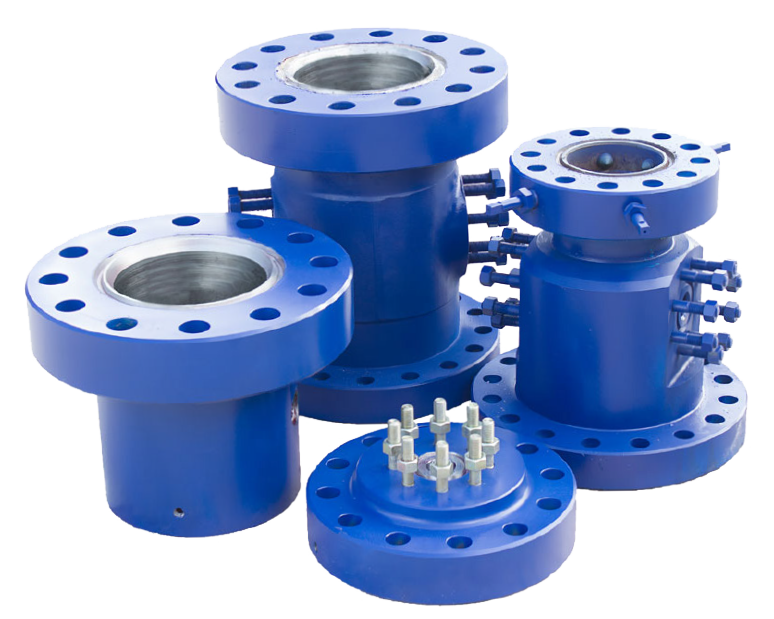
Wellhead Products
MISCELLANEOUS
At Forged Components, with our manufacturing capabilities, we design and produce custom forged wellheads that are specific to your requirements, providing solutions for unique pressure ratings, sizes, shapes, and material needs. The manufacturing process involves several intricate steps, combining traditional forging techniques with modern engineering and manufacturing practices. This process ensures that the wellhead can withstand the extreme pressures, temperatures, and corrosive environments often encountered in oil and gas extraction. Here’s an overview of how our custom forged wellheads are manufactured.
Design and Engineering
Specification Review: The process begins with a thorough review of the customer's specifications, including pressure ratings, temperature conditions, sizes, and material requirements.
CAD Modeling: Engineers design the wellhead using Computer-Aided Design (CAD) software, creating detailed models that adhere to the specified requirements and industry standards.
Material Selection
Material Procurement: Based on the design specifications, the appropriate raw materials (usually steel or specialized alloys) are selected for their strength, corrosion resistance, and suitability for operating environments.
Material Preparation: The raw materials are prepared for forging, often cut into billets or preforms that approximate the shape of the final product.
Forging Process
Heating: The preformed materials are heated to a high temperature, making them malleable and ready for shaping.
Pressing or Hammering: The heated material is then pressed or hammered into shape. This can be done using a variety of forging methods, such as open-die forging, closed-die forging, or ring rolling, depending on the part’s complexity and the required precision.
Trimming and Finishing: Excess material is trimmed off, and the forged parts are subjected to finishing processes, such as machining, to achieve the precise dimensions and surface finishes required.
Heat Treatment
Process: After forging, the components undergo heat treatment to improve their structural properties, such as strength, toughness, and hardness. The specific heat treatment process (annealing, quenching, tempering, etc.) depends on the material used and the desired properties of the final product.
Machining and Manufacturing of Additional Components
Precision Machining: Forged components are machined to achieve close tolerances and surface finishes that meet the design specifications. This step may involve CNC (Computer Numerical Control) machining, drilling, milling, and other machining processes.
Manufacturing of Additional Components: Wellheads consist of several components, such as flanges, valves, and connectors. Some of these components may be manufactured separately through similar processes and then assembled into the final wellhead assembly.
Inspection and Quality Control
Dimensional Inspection: Components are inspected for dimensional accuracy using precision measuring tools.
Material and Mechanical Testing: Various tests, including tensile strength, impact resistance, and hardness tests, are conducted to ensure the material meets the required specifications.
Non-Destructive Testing (NDT): Inspection techniques such as ultrasonic testing, magnetic particle inspection, or radiographic testing are used to detect potential internal defects without damaging the components.
Assembly
Component Assembly: The forged and machined components are assembled into the final wellhead structure, often including the installation of seals and testing of the assembled wellhead to ensure leak-proof performance.
Testing: The assembled wellhead undergoes pressure testing and other functional tests to verify its integrity and performance under simulated operating conditions.
Finishing and Coating
Surface Finishing: The wellhead may receive surface treatments such as sandblasting, painting, or coating to enhance corrosion resistance and longevity.
Marking and Identification: Finally, the wellhead is marked with identification numbers, pressure ratings, and other relevant information for traceability and compliance with industry standards.
Delivery
Packaging and Shipping: The finished wellhead is packaged securely and shipped to the customer, ready for installation.
Custom forged wellheads are essential for the safe and efficient extraction of oil and gas, and their manufacturing process reflects the critical nature of their application, requiring precision, expertise, and strict adherence to industry standards.

